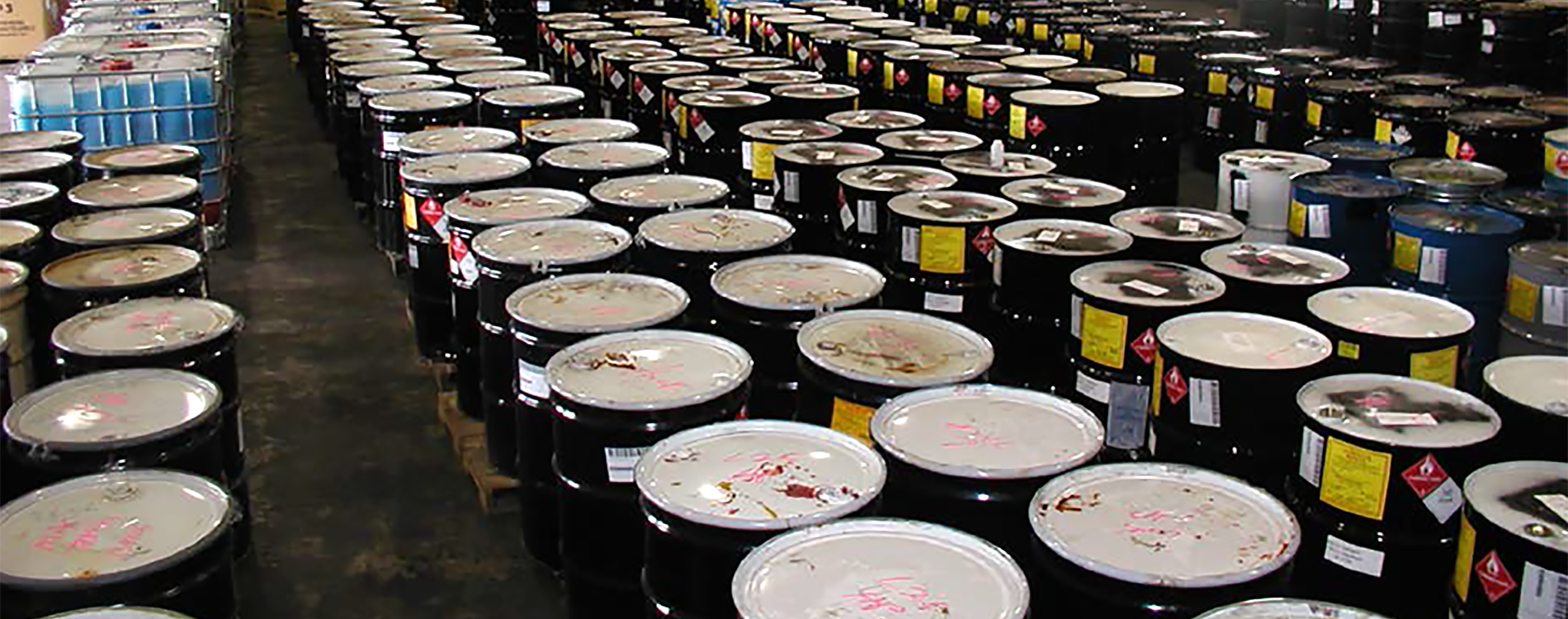
Sustainable practices
In addition to our operations, we also provide important environmental services to our community. This includes our used oil and used paint and paint-related materials collection program held annually on Earth Day, and the use of yard waste in our emerging artificial soils project
We are industry leaders in developing process technologies which are implemented at our site, and research and development for new technologies is continuing at the plants.
Read more about Continental Cement and Green America Recycling’s efforts in our latest Corporate Social Responsibility brochure.
Recycling and manufacturing
Green America Recycling’s staff of chemists and technicians operate a fully equipped state-of-the-art on-site fuels laboratory to ensure employee safety and regulatory compliance.
Before a potential waste stream is approved for shipment, a stringent prequalification analysis is performed to ensure that the material is compatible with the cement-manufacturing process and meets acceptance criteria for chlorine, BTU, organic compounds and metals.
Any fuels that do not meet acceptance criteria are rejected. We do not accept regulated medical waste, dioxin, PCB or radioactive waste streams. Our current reject rate is less than 1 percent.
Special handling requirements are also determined by complete review of material safety data sheets (MSDS), supplier information and thorough laboratory analyses.
Incoming shipments are again tested upon arrival and prior to off-loading to verify conformance with established waste profiles and permit specifications.
A final lab test confirms that all blended wastes, both hazardous and non-hazardous, comply with cement manufacturing requirements and government standards for burning hazardous waste (40 CFR 266), before they are fed to the kiln.
All kiln inputs (coal, raw material feed, and waste fuel) are sampled and analyzed prior to burning. Kiln outputs (cement and kiln dust) are also sampled and tested. TCLP tests are performed on kiln waste dust to confirm that no metals will leach into the groundwater.
Lab approval forms must be provided to the control room operator before any material is released for use in the kiln. As an added safeguard, metal and chlorine concentrations are entered into a computer network which, by using minute by minute feed rates, verifies that those concentrations are well within the permitted limits.
In addition to the waste materials recycled for fuel by Green America Recycling, Continental Cement also recycles industrial waste by-products and utilizes them in the cement manufacturing process.
These recovered by-products, coupled with the locally available raw materials, help us manufacture cement in a sustainable way. Listed below are the recovered waste materials that we use to make cement and preserve natural resources.
- Synthetic Gypsum – Calcium sulfate scrubber stone from a local power plant, recycled to replace and preserve natural gypsum (7 percent of finished cement or 168,000,000 pounds annually)
- Iron – Recycled material from local steel mills to replace and preserve natural iron ore reserves (1.5 percent of finished cement or 36,000, 000 pounds annually)
- Bottom Ash – Coal ash reclaimed from local industrial power plants
- Aluminum Oxide – Polishing agents and catalyst materials reclaimed from local equipment manufacturers
- Sodium Bicarbonate – Polishing agent reclaimed from a local equipment manufacturer
- Cement Kiln Dust – Dust captured from the cement manufacturing process that is reintroduced into the process in order to minimize waste and reduce energy consumption. We recycle 100 percent of the dust; excess cement kiln dust is used for solidification
Reclamation
Continental Cement pursues every practical opportunity to reclaim its on-site quarries with native grasses and trees and return them to natural habitat as soon as possible. We have reclaimed more than 200 acres of quarry land to natural habitat with traditional methods.
And, as an added benefit to employees, an old shale quarry was converted into a 30-acre lake with a picnic site and recreational fishing.
Sustainable and LEED-Oriented Products
Concrete, with cement as its primary ingredient, remains the 2nd most widely-used, man-made, construction material on earth.
Concrete is 100 percent recyclable, and will not rust, rot or burn. Plus, its unique ability to be formed into any shape makes it a natural choice for residential, commercial and public construction. Concrete can be colored, stamped and textured making it a durable, safe and sustainable material for any application. Continental Cement’s distribution terminals along the Mississippi River provide efficient river transportation to our concrete producing customers, thereby eliminating roughly 13,000 semi-trucks from our highways each year.
Using our cement helps engineers and architects, who pursue Leadership in Energy and Environmental Design (LEED) certification, benefit from locally distributed cement that contains a significant amount of recycled materials.