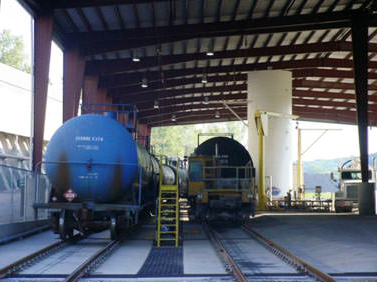
Liquid Fuel Program
Liquid fuels are unloaded directly into one of six waste fuel blend tanks. A vapor balancing system is utilized between tanks and trucks during off-loading.
Venting is through a carbon canister. The liquids, with dispersed solids, are placed in one of two kiln feed (burn) tanks. The tank contents are analyzed for regulated constituents and injected into the burn zone of the kiln. A burn tank will typically take about 24 hours to empty. The dispersible program depends upon liquid stored within the tank farm to be used as a diluent for dispersing the solids and sludge in the hydropulper. Acceptable materials for this program include, but are not limited to: solvents, paints, degreasers, oils, alcohols, and other off-spec products.
Dispersible Fuel Program
Dispersible solids and sludge are processed in a drum auger/decanter system. Drums are loaded onto a conveyor, and then lifted by an elevator to the drum auger. Any solids that do not fall out into the screw conveyor feeding the drum decanter are augured out, rendering the drum RCRA empty. These solids are blended with liquid fuels in the liquid receiver tank and are then pumped back to the fuel farm.
Acceptable materials for this program include, but are not limited to: sludge, tank bottom waste, centrifuge solids and waste water in roll-offs.
Solid Fuel Program
The dry solids program consists of off-loading, storage, material preparation for debris-like solids and monolithic drums, originating from both received bulk shipments and containerized debris in drums and boxes.
Examples of acceptable materials include: rags, wood, and off-specification products, with limited free liquids. They are dumped and fed with a front-end loader to a three stage, nitrogen-inert shredder. The granulated, waste-derived fuel is then placed in piles, ready to be fed to the kiln. The individual piles are analyzed for regulated components and loaded into a sealed wagon for transport to the dry solid “feed processing” building where the material is pneumatically conveyed to the kiln through a separate feed pipe to the low NOx burner in the pre-calciner.